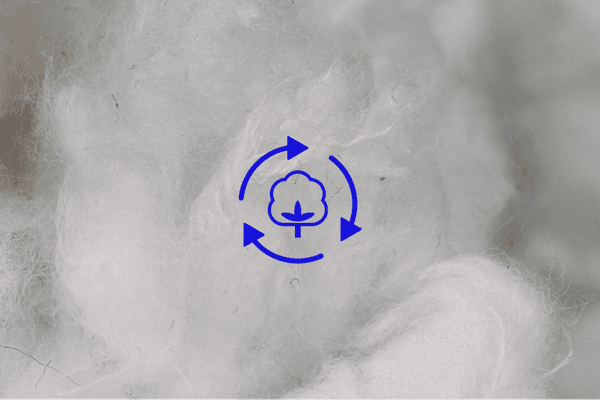
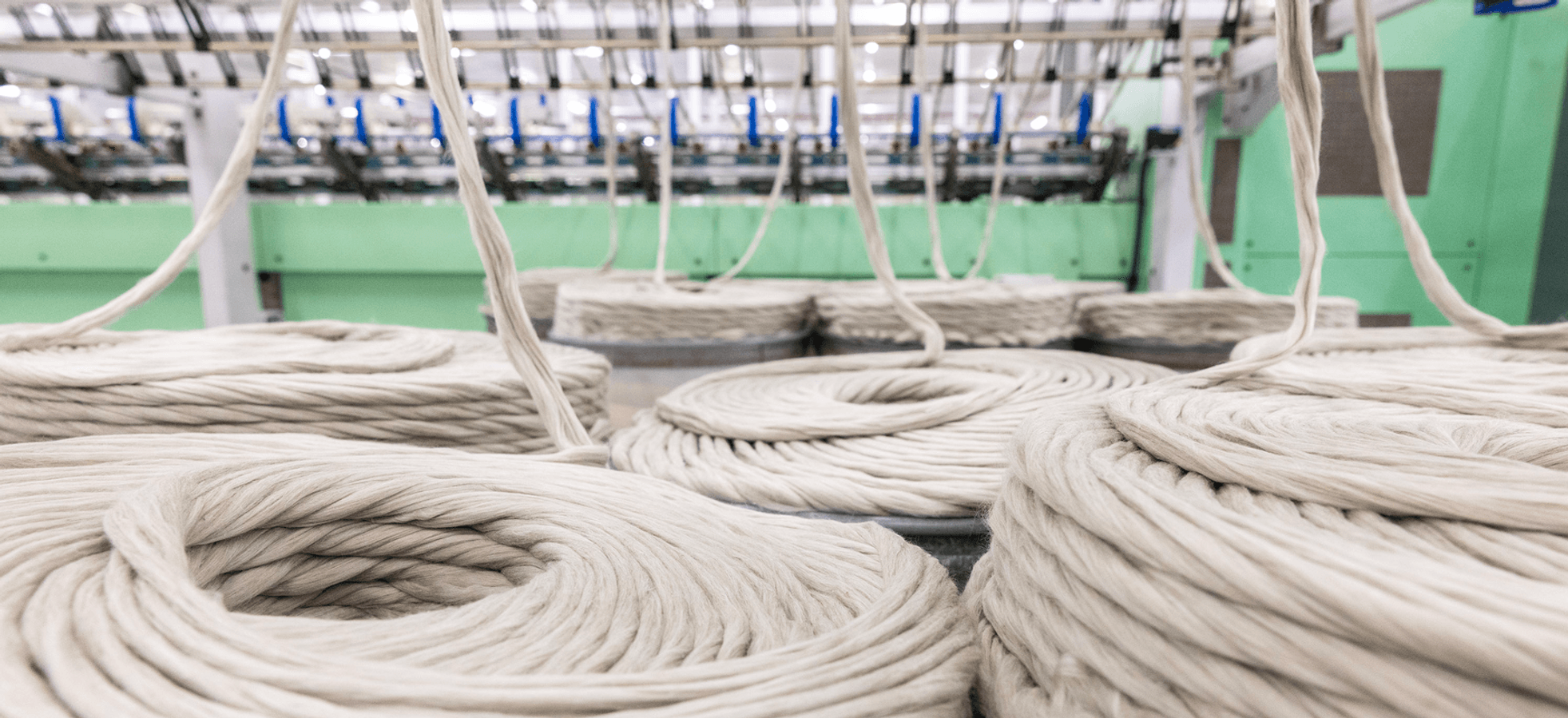
At Recover™, we produce high-quality recycled cotton fibers and blends for the fashion industry. As a tier 4 supplier in the fashion supply chain, our direct clients are spinners who transform our fibers into recycled cotton and blended yarns. Our team of passionate experts in materials science, textiles, fashion, and sustainability collaborate closely with our spinner partners to seamlessly integrate our recycled fibers into their processes. For those not familiar with the industry, here’s a quick and easy summary of the different spinning techniques and how we measure our cotton yarns.
What is Textile Spinning?
Spinning transforms raw textile fibers into yarn, a process which, for thousands of years, was done by hand. However, modern spinning uses advanced machinery and a range of different techniques tailored to the type of yarn being made. During the spinning process, fibers are drawn out, twisted together, and wound onto a bobbin. Once the yarn has been produced through spinning, weaving can take place in order to create fabric.
Cotton is one of the most widely used fibers for spinning, along with viscose, wool and synthetic polyester. For mechanically recycled fibers, there are two main types of spinning: open-end and ring spinning.
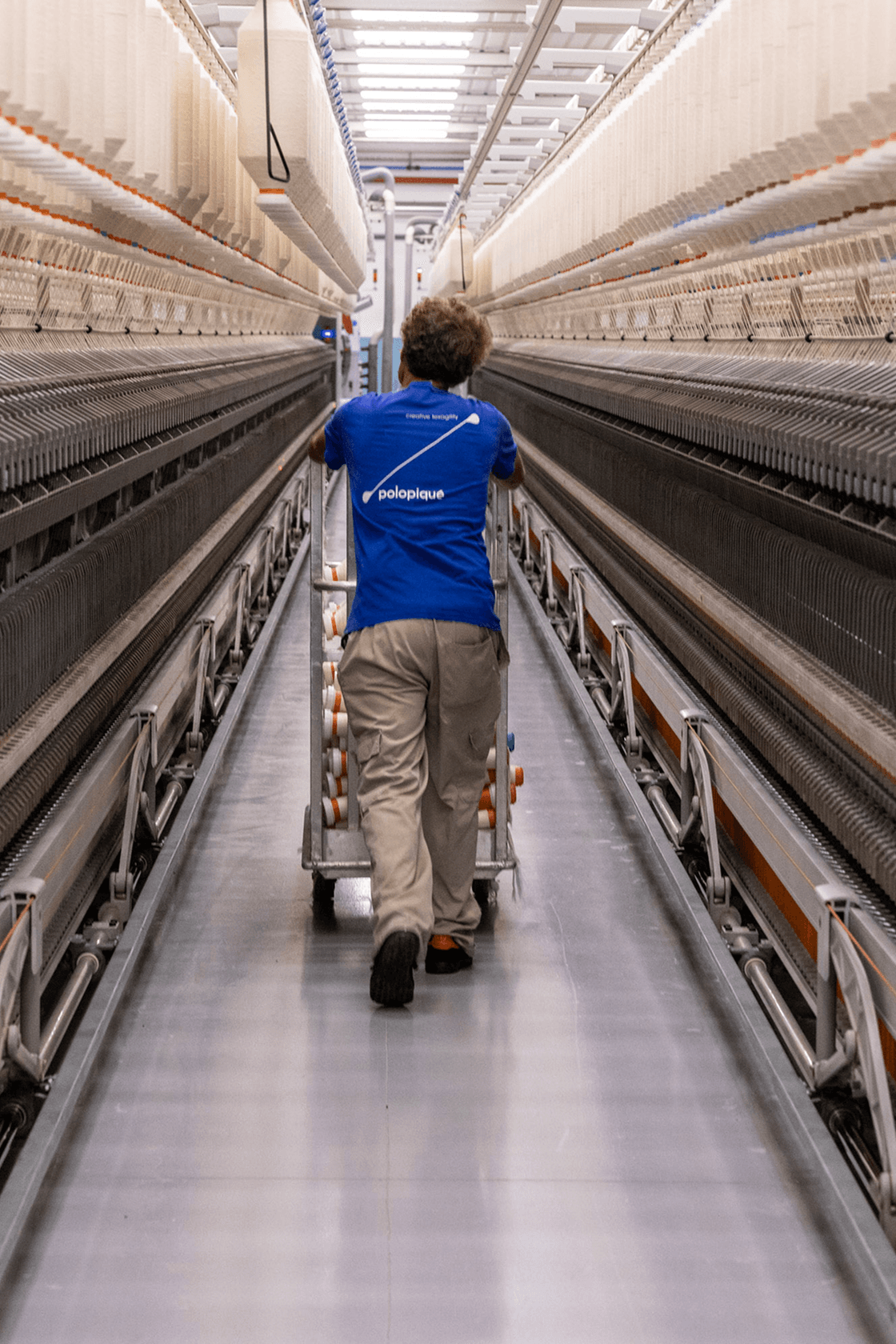
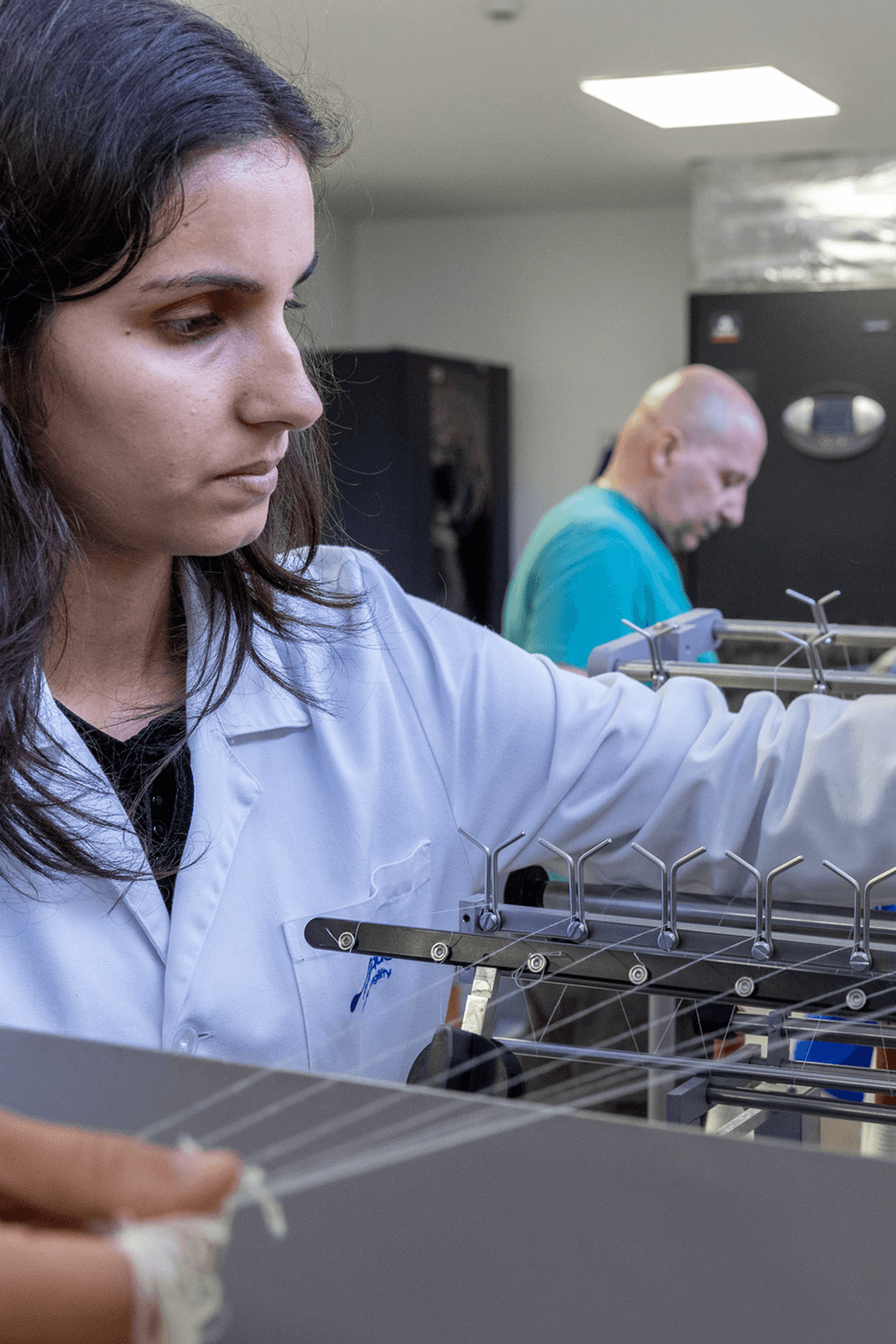
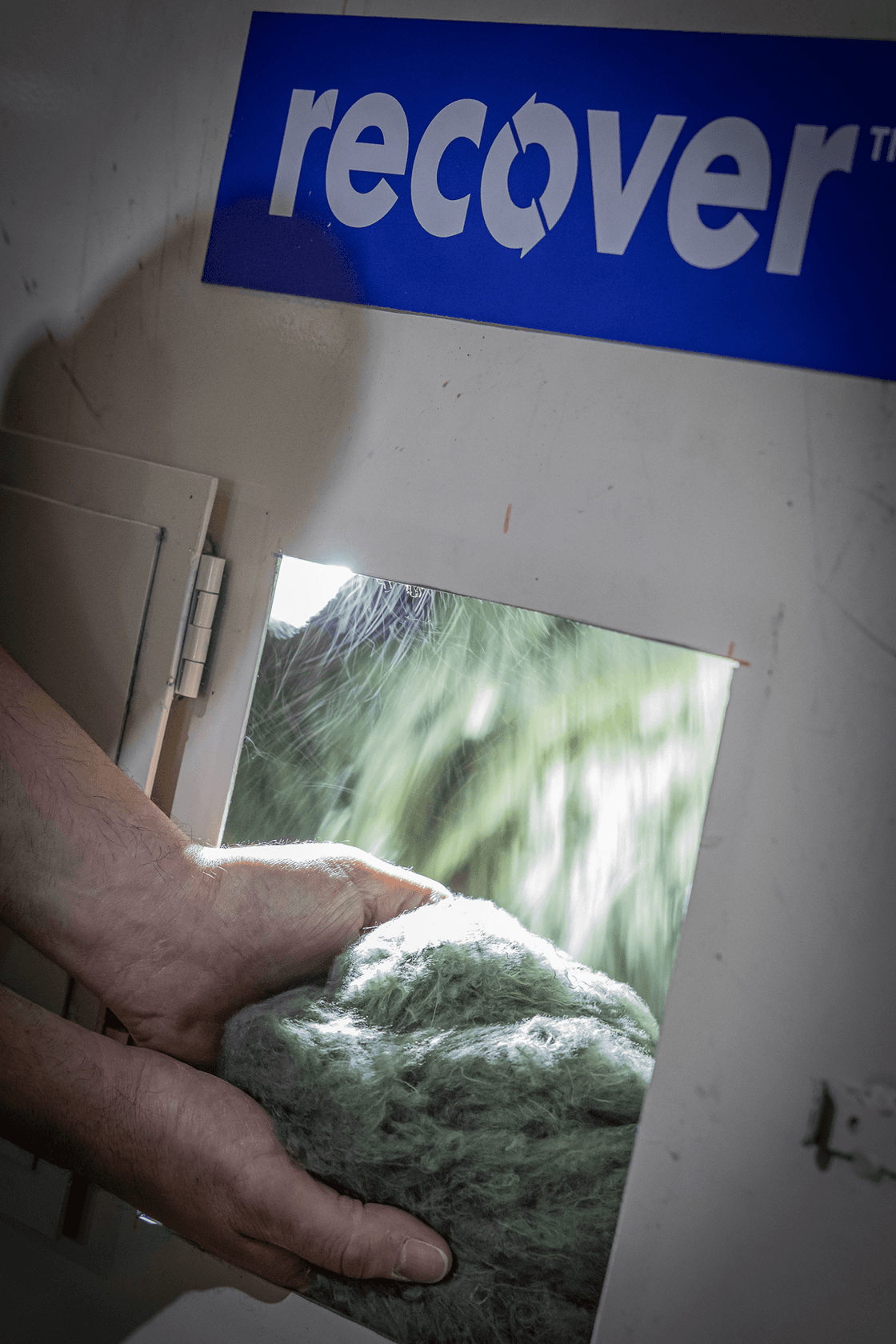
Open-End Spinning
Open-end spinning, also known as rotor spinning, is a type of modern spinning which creates yarn without the need to use a spindle. At the heart of the open-end process is a rotor, wherein fibers can be collected and then drawn off as a yarn.
Open-end spinning machines start with a combing roll that prepares the fiber sliver. The combing roll rotates at high speed and introduces the fibers into the rotor, where they will be twisted into yarn. The fibers are transported to the rotor by air suction. Most rotors have a “groove” - a shallow, U- or V-shaped channel around the inside edge of the rotor - to align the fibers. The rotor twists the fibers together to form yarn, in a continuous and self-sustaining process. It is called “open-end” spinning because the fibers are kept loosely separated before being twisted together at the open end of the rotor to form the yarn. This separation allows for better control over the twisting process and means that the technique is faster and more efficient.
Unlike traditional ring spinning, which requires multiple steps, open-end spinning offers a more streamlined process as you only need to do the drawing process (stretching and thinning out the fiber sliver) once. This makes it an ideal method for producing heavier yarns like those used in denim. Open-end spinning offers a highly versatile option, working to process different types of fibers - including cotton, wool and viscose - into yarn. It also allows for careful control of the yarn down to the thickness, texture and appearance.
Key Characteristics of Open-End Spinning
- Fast and efficient process
- Generally rougher and less refined than ring-spun yarn
- Best suited for heavy, durable fabrics and cost-effective production e.g. denim, basic t-shirts, home textiles or industrial textiles
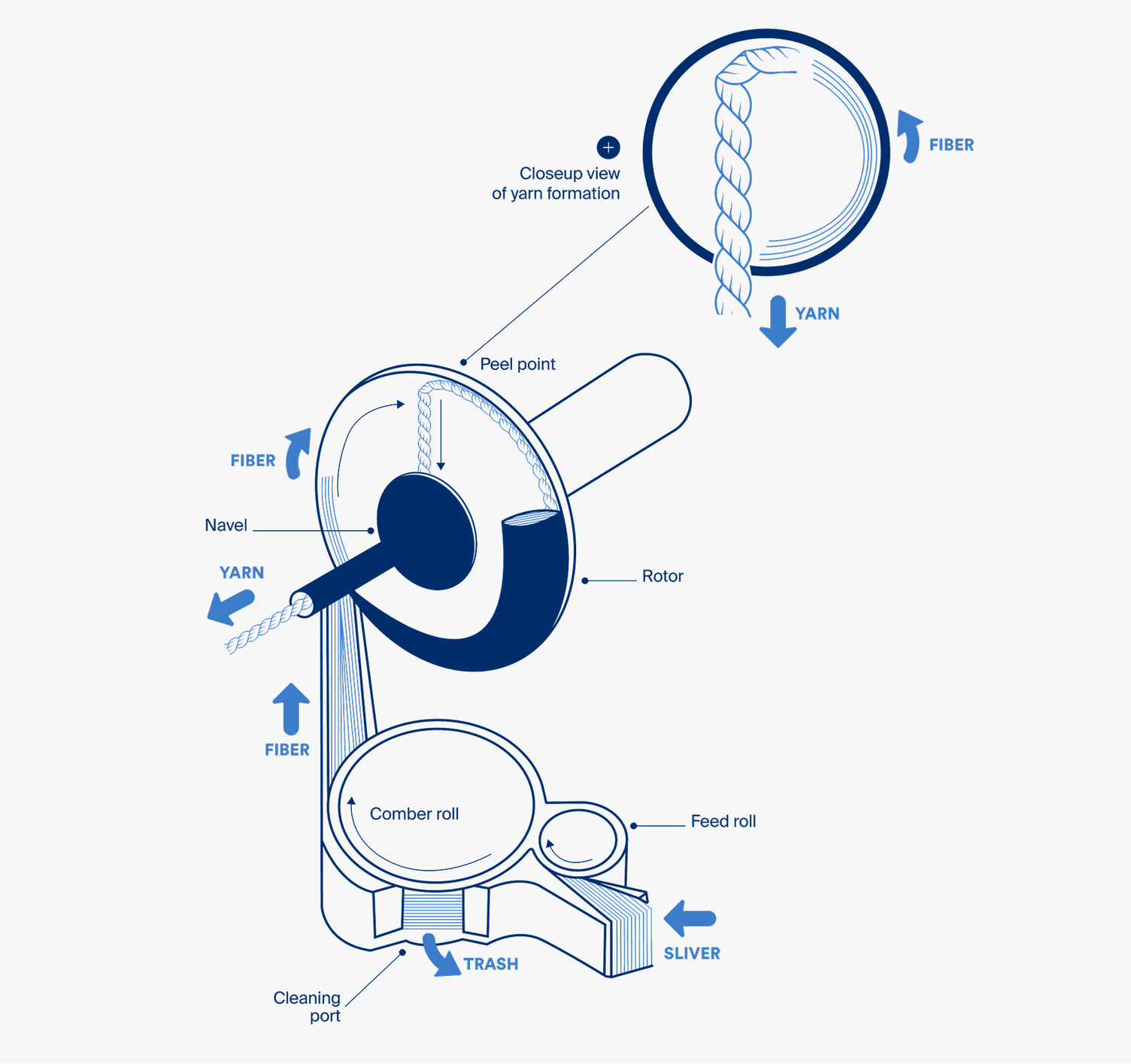
Ring Spinning
Ring spinning is a traditional method widely used in the production of high-quality yarn. During this process, slivers must be drawn out to make them thinner and more uniform. The first step is carding, which is crucial as it separates, cleans, and straightens the fibers, blending different fibers together to create a uniform material. This ensures that the fibers are properly aligned and ready for spinning into thread or yarn. The card sliver is then stretched and given a slight twist to hold the fibers together during the draw frame and roving steps. An additional step, combing, can be added after the first draw frame. Combing is used for high-quality yarns to remove short fibers, neps, and impurities, resulting in a smoother, finer, and more uniform yarn.
Ring spinning begins with drafting, where the roving is passed through rollers at different speeds to stretch and align the fibers, reducing irregularities. The stretched fibers are then twisted together by a rotating spindle and guided through a ring that holds a traveler—a moving metal component that controls the tension and ensures a strong and continuous yarn. Once finished, the yarn is wound onto a bobbin in layers, ready for the next step of textile production.
Ring spinning is known as the most difficult method of spinning. Although there is a myth that recycled cotton cannot be ring spun, at Recover™, we have refined our process to keep fibers as long as possible, making them suitable for ring spinning.
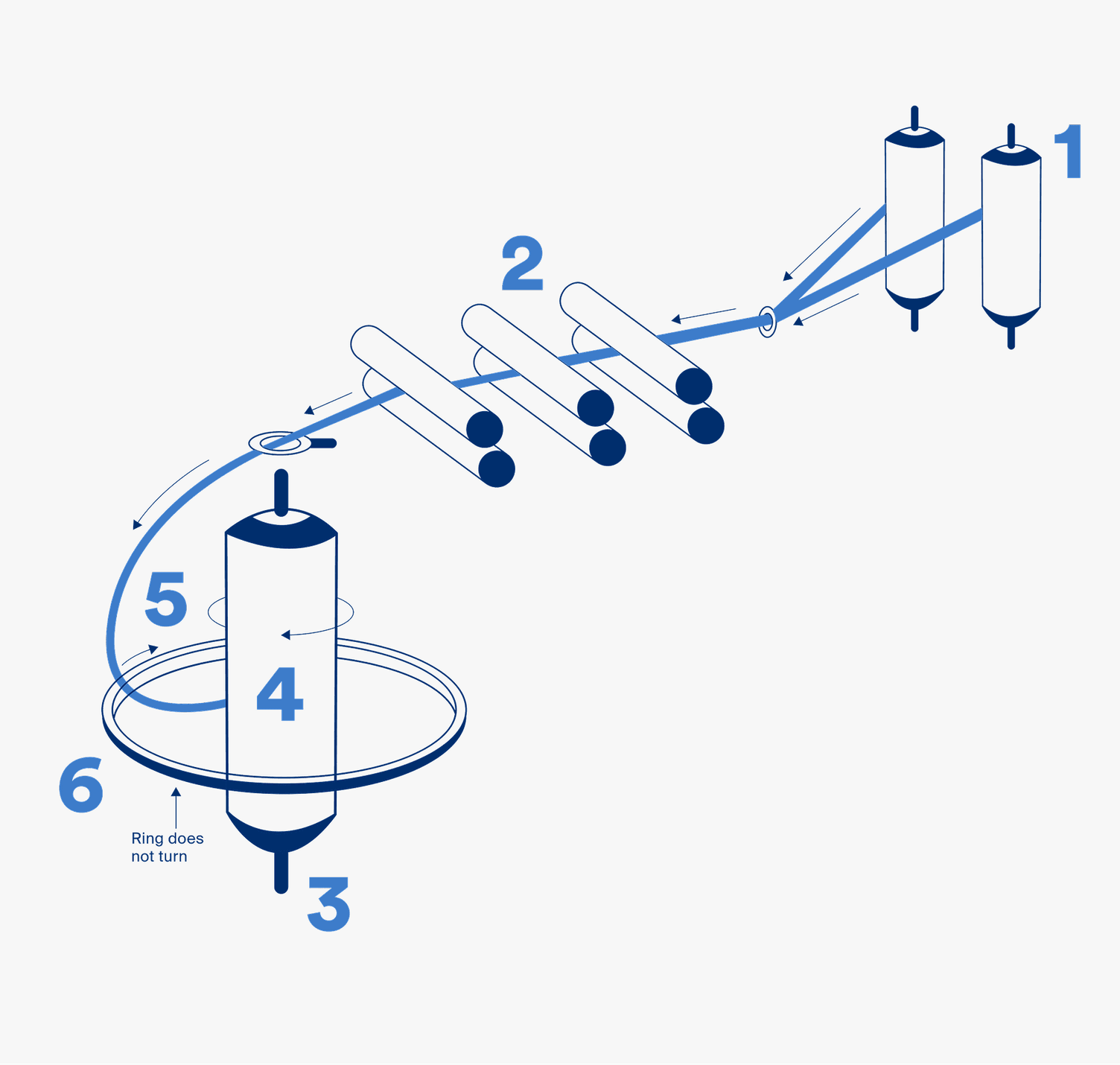
Yarn applications
The “yarn count” calculates how thick the yarn is and is measured by mass per unit length. Within the spinning industry, the yarn count is known as “Ne”. Finer yarns have a higher Ne number whereas thicker yarns have lower numbers (between Ne 4 and Ne 20).
- Ne 1-6: Typically used for very thick yarns, often used in heavy-duty fabrics, rugs, or carpets.
- Ne 6-20: Used for heavier yarns suitable for upholstery fabrics, denim, or other heavy garments.
- Ne 20-30: Commonly used for medium-weight yarns suitable for a wide range of fabrics including t-shirts, dress shirts, and lightweight woven fabrics.
- Ne 30-40: Used for finer yarns suitable for lightweight woven fabrics, dress shirts, or other garments requiring a finer texture.
- Ne 40 and above: Used for very fine yarns, often used in high-quality dress shirts, delicate fabrics, or for specialized applications like fine lace.
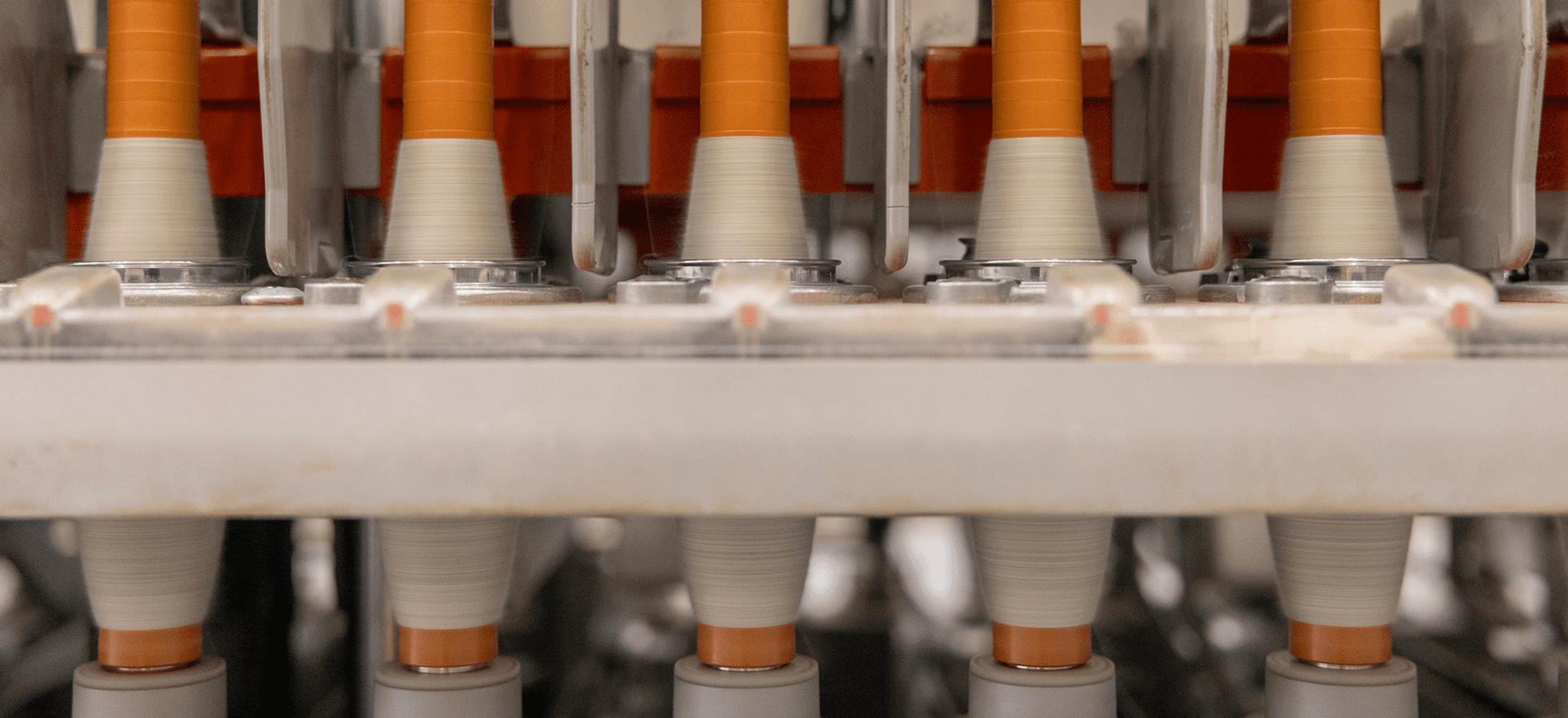
The Role of Spinning in Textiles Production
Spinning is a key component of textile manufacturing - transforming raw fibers into yarn that is the basis for all fabrics. From more traditional methods like ring spinning to approaches relying on modern machinery, like open-end or compact spinning, each technique has its own applications. Understanding the differences between the types of spinning helps manufacturers choose the right process for their desired fabric when it comes to strength, quality and cost-efficiency. As technological advances continue to be introduced, spinning methods will keep evolving, giving increasingly more options for sustainable fabrics.
You may also be interested in
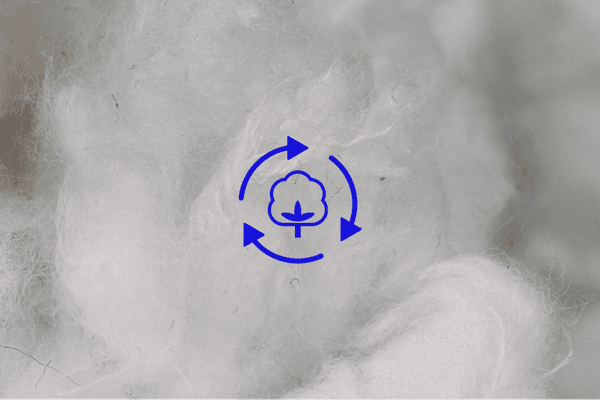
