
Zero-Waste Innovation: Transforming Cotton Dust into Compostable Packaging with Ecovia
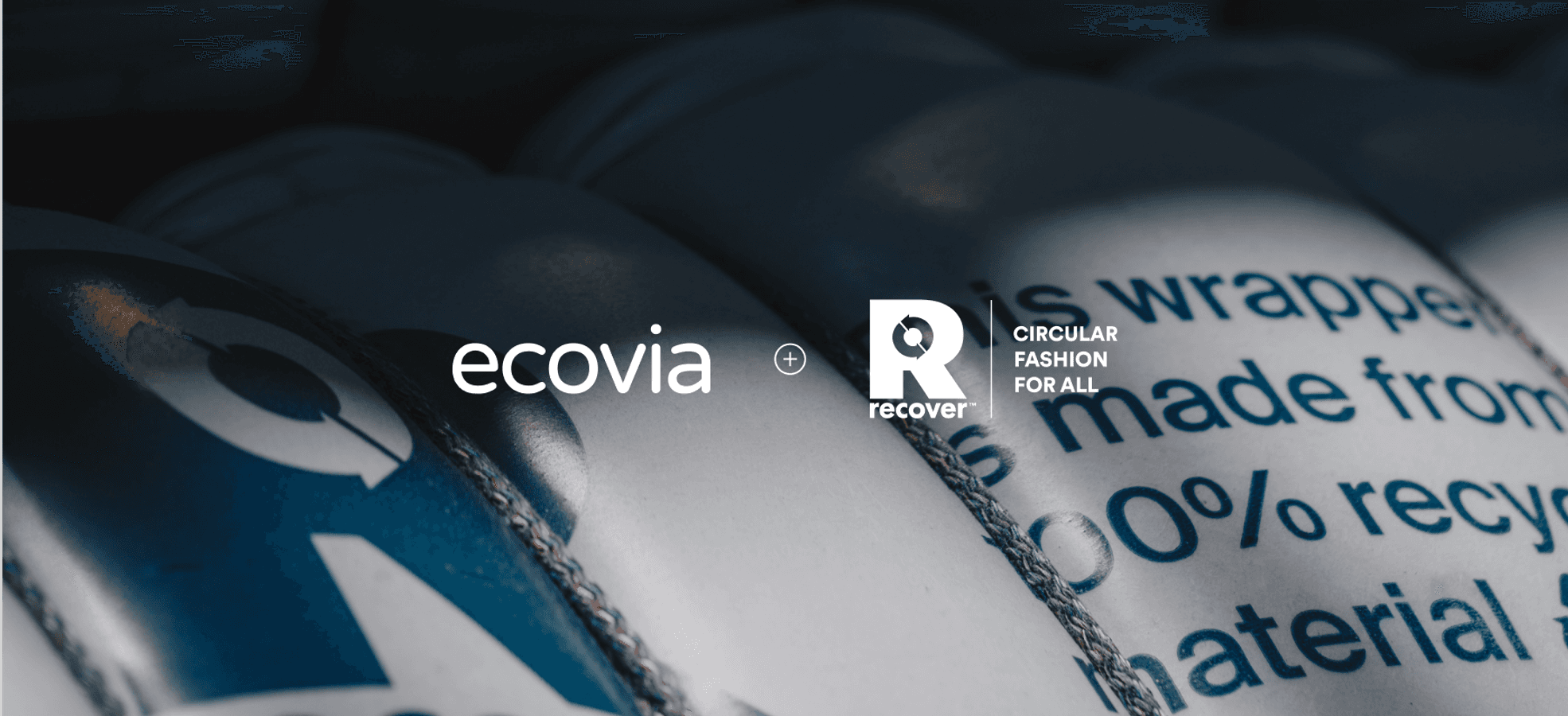
Recover™ aims to become a zero-waste company, minimizing the generation of waste and maximizing the recovery of waste produced through our own operations. In line with this commitment, we segregate and track all the different waste flows in our production hubs and are identifying and implementing opportunities to reduce and recycle our waste.
Recover™, like all other mechanical recyclers, generates a by-product often referred to as “cotton dust”. It is composed of all the short fibers, generally smaller than 4mm, that cannot be integrated in our final product because it might compromise the quality of our premium recycled cotton fiber. Across the entire production process, short fibers are pulled out and separated by the extraction system to leave the long fibers - our main product - clean.
At Recover™, we never see waste - we always see opportunities. That’s why we saw the potential in this dust and gave it a name: RParticle.
During 2023, Recover™ was focused on consolidating recycling options for the RParticle to add value for different industries: construction, paper, or even chemical recyclers.
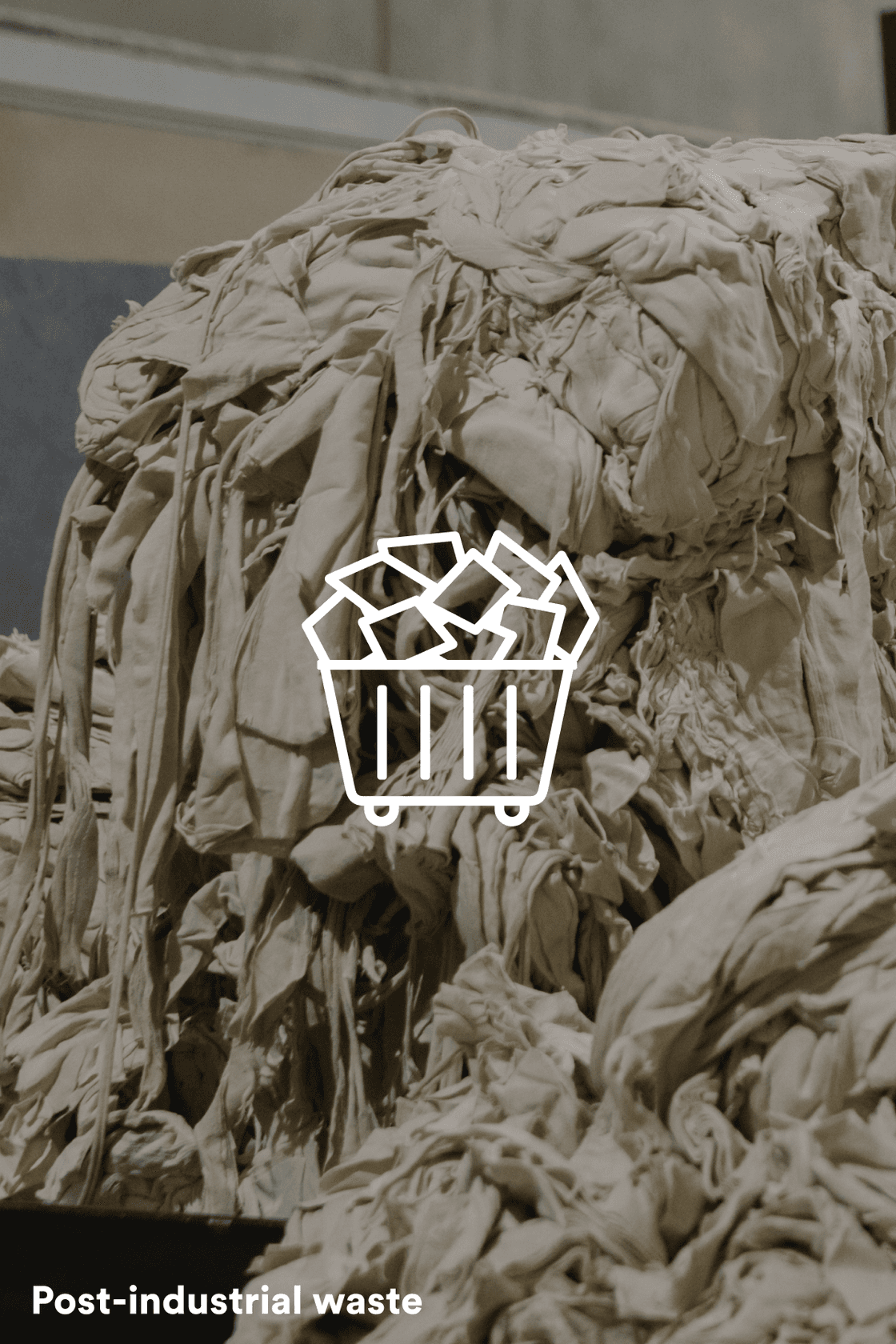
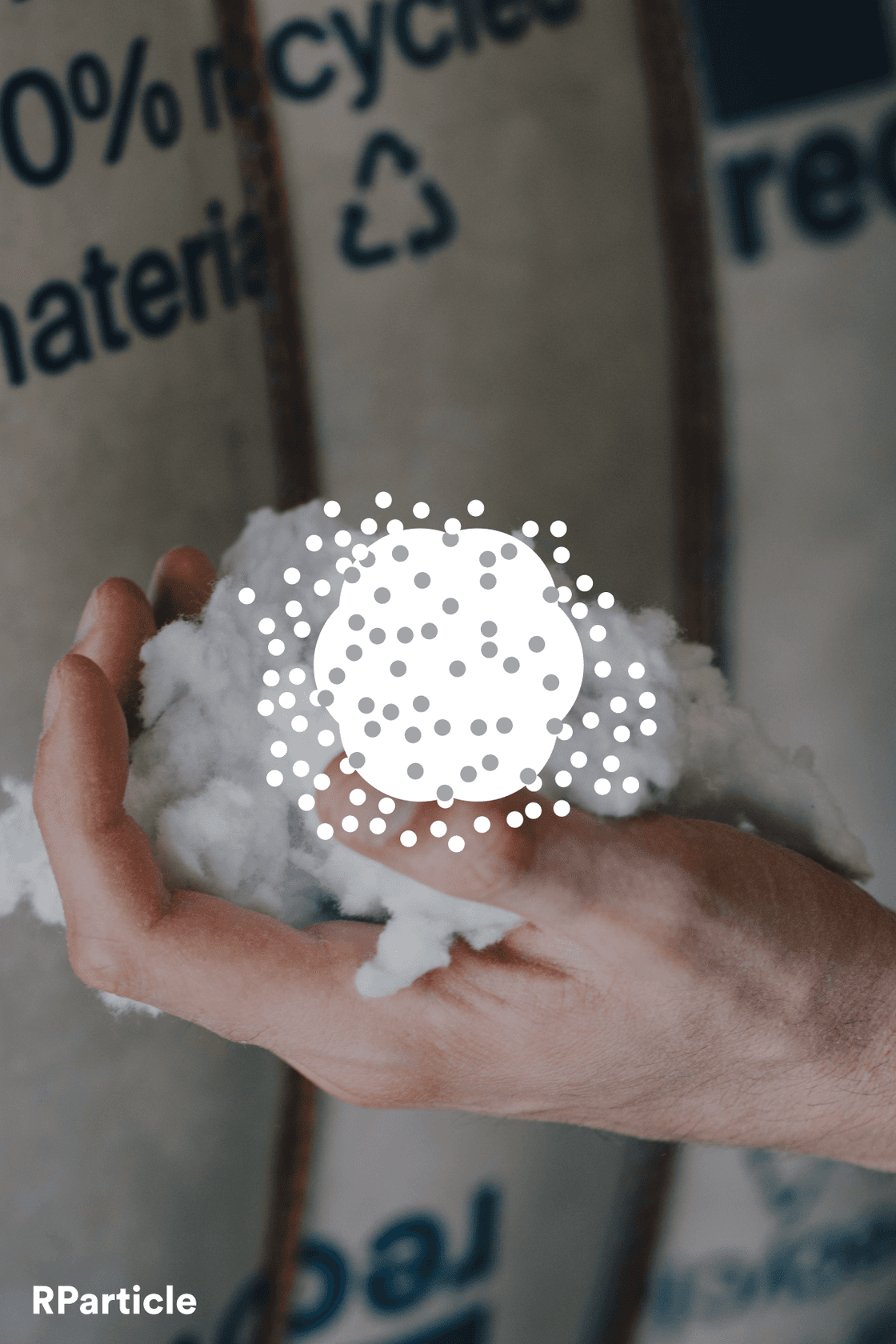
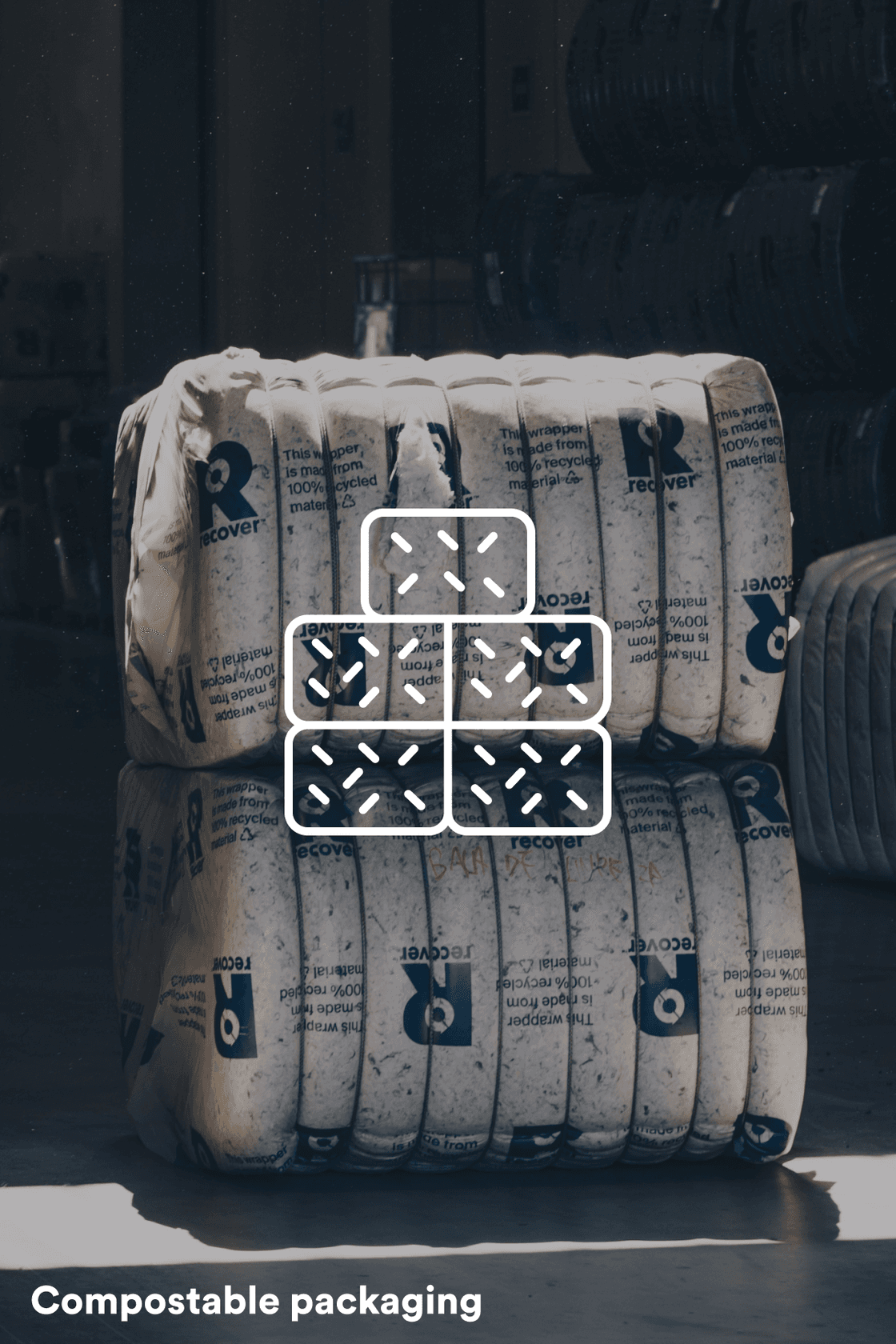
Waste to worth: Finding value in cotton dust
While searching for a suitable large-scale recycling solution suitable for our fiber dust, we have been able to integrate a small-scale R&D development into our process that gives our by-product a new life. In partnership with Ecovia, a clean-tech startup that uses garment waste to create compostable packaging, we are able to incorporate RParticle - our cotton fiber dust - into our recycled fiber bale packaging.
Ecovia typically uses garment waste in their processes. They usually source pre-consumer apparel waste from the garment industry. After cleaning, sorting, and processing it to extract cellulose fiber through a chemical process, they break down the output to convert it into a bio-based material, that can then be transformed into compostable films, suitable for various type of packaging such as grocery bags or anti-static packaging for electronics.
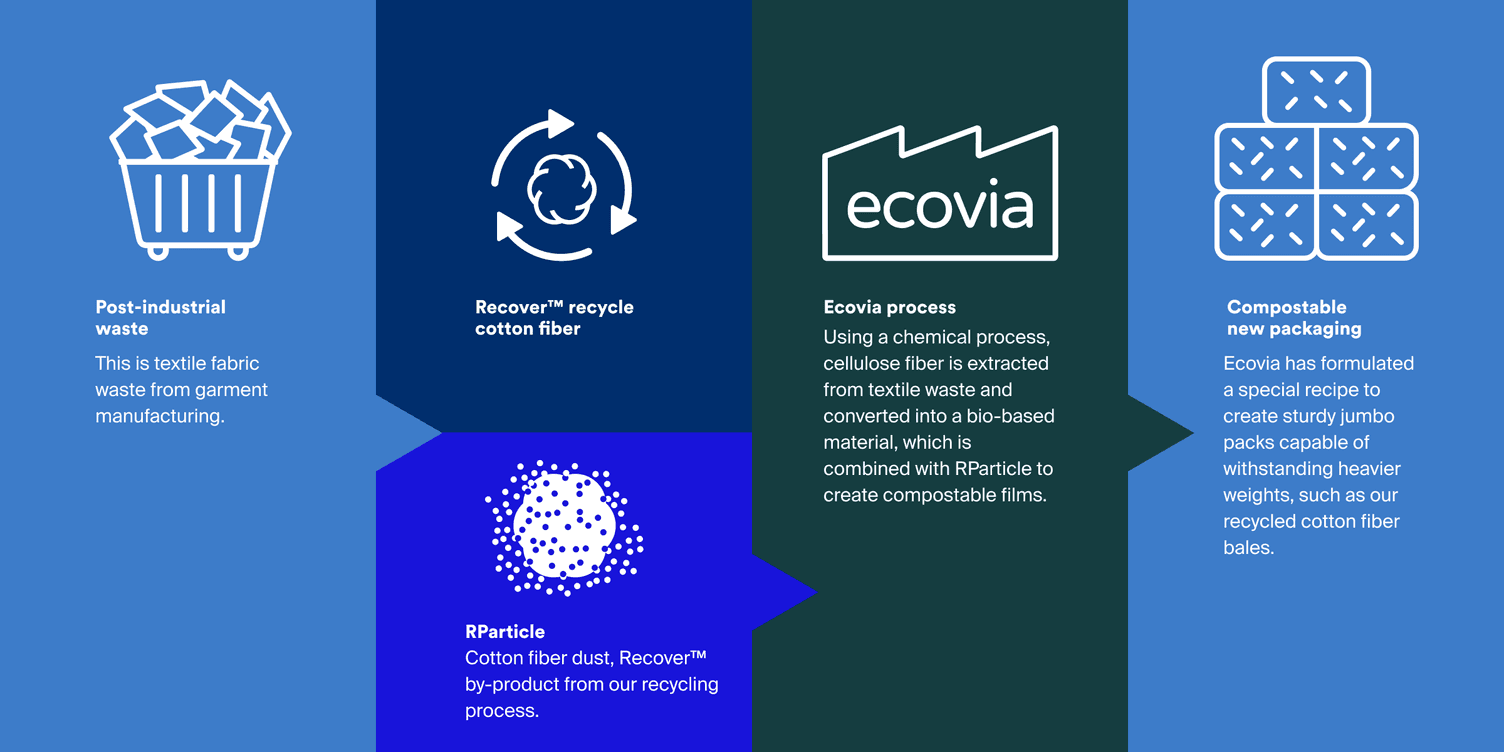
Circularity, right down to the packaging!
For Recover™, Ecovia has formulated a special recipe which can make sturdy jumbo-packs (bale wraps) to withstand higher weights, like our recycled cotton fiber bales. To make it, they use our RParticle as one of the components, mixed with two durable materials to form a strong bond.
The result is a reliable compound which can be stretched into thin film layers. Thanks to this, we can offer Recover™ customers sustainable packaging solutions which are durable and reliable.
Ecovia’s tailored solution for Recover™ saves roughly 4.53 kg CO₂ eq per bag compared to standard reusable plastic bags.
A typical reusable bag - made from High-Density Polyethylene (HDPE) - generates around 6.92 kg of CO₂ eq for every kilogram produced. Ecovia’s compostable packaging only creates around 2.39 kg of CO₂ eq per kilogram, due to its mostly plant-based composition.
Through our partnership with Ecovia, we are also able to tell a story: even recyclers can be challenged to close the loop. The packaging created by Ecovia uses our own waste and transforms it into something of value.
We are always striving for even more innovative solutions. Recover™ often partners with universities and research institutes to test and develop the potential high value options for our RParticle - cosmetic, food industries, bioplastics. In-house our team keeps working tirelessly to find circular solutions for our waste streams and bring us closer to a zero-waste future.
Discover more about our waste streams and zero-waste initiatives in our sustainability report 2023.